


UC team restores boy’s use of his arms
Engineering students in San Diego develop device for 5-year-old with a rare condition.
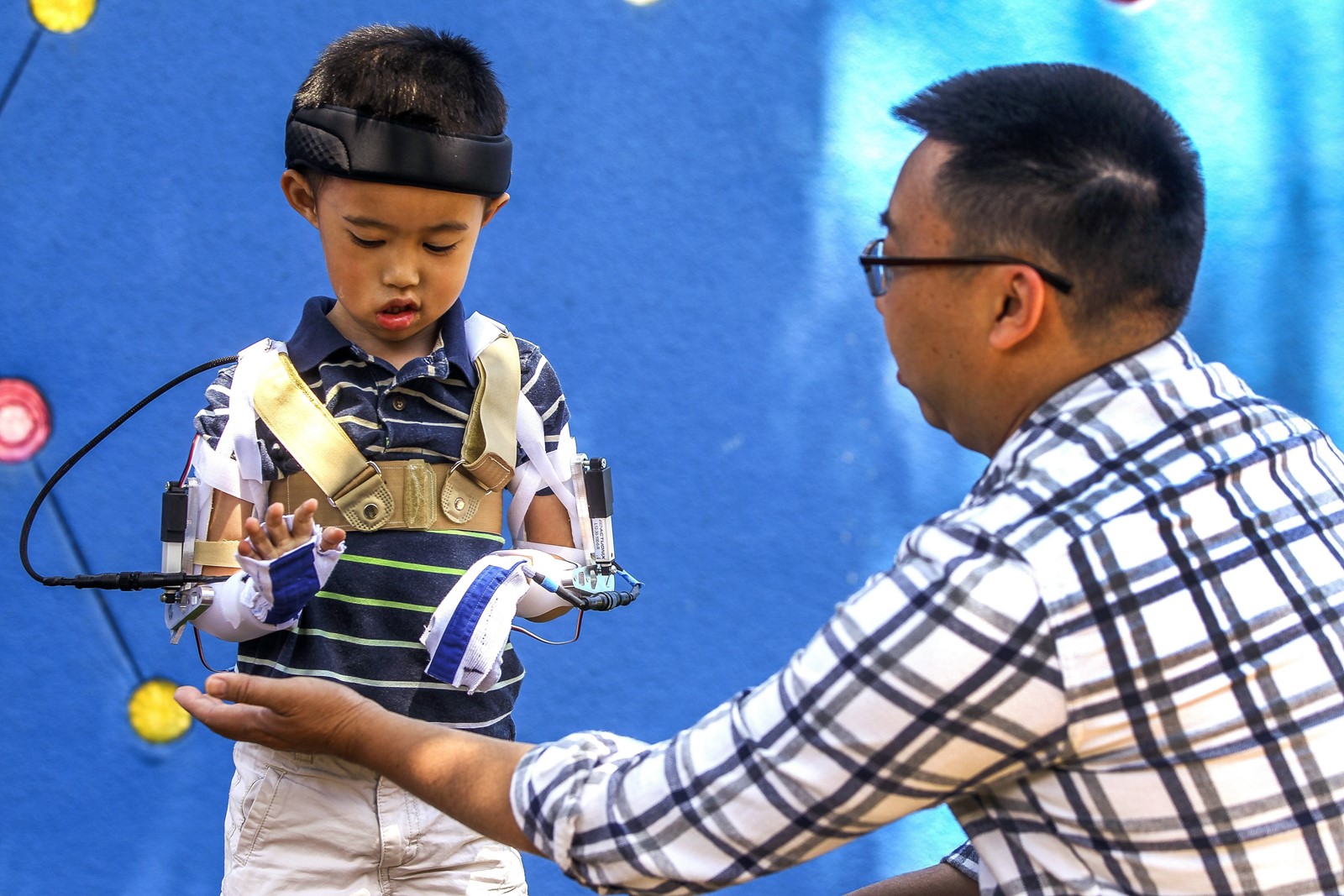
But a device built by four UC San Diego engineering students delivers just the help he needs to reach out and touch the world.
With cameras watching Friday morning at Rady Children’s Hospital, Max was strapped into a pair of motor-assisted orthotic braces, his fingers sliding into sensor-loaded gloves.
Once the contraption was in place, tilting his wrist up caused his arm to raise, bending at the elbow. Tilting down accomplished the opposite motion, and Max was quick to start roughhousing with his father, Dr. Ted Ng, landing a few light punches before grabbing his dad’s nose.
While that kind of play drew laughs, Ng said he has been looking forward to a slightly different maneuver that has been difficult for his boy to accomplish.
“One of the things I missed the most is him just grabbing me for a hug,” Ng said. “It just feels nice, you know, to have him wrap his arms around you.”
Max is one of more than 500 kids nationwide who have experienced such symptoms since 2014. His condition, called acute flaccid myelitis, is thought to be caused by infection from viruses in the same family as the germ that causes polio.
Researchers have yet to determine why most kids are unaffected, but a few end up with nerve damage, quickly stealing use of arms, legs or other body parts with a cruel randomness that is at once mystifying and potentially deadly.
Dr. Andrew Skalsky, a rehabilitation medicine physician at Rady, said Max is rare among AFM patients. The boy retained full control of the muscles in his wrists and hands even as the motor nerves attached to the major muscles in his arms and shoulders have atrophied. Wrist and finger dexterity intact, Max has developed ways to raise his arms, pushing them up with his knees to bring his hands close to what he wants to grasp.
But certain tasks, such has hugging his parents or young sister, remain out of reach. Those kinds of movements require lifting both arms simultaneously, a task that’s difficult if you’re using your knees to do the lifting.
Skalsky said using some sort of motorized brace to do the work Max’s muscles can’t has seemed like a great idea for some time. But existing braces, with beefy frames and large motors, have been too heavy to do the job.
“His shoulder girdle muscle isn’t there anymore, and just the weight of the brace alone, even without the motors, would dislocate his arm pretty easily,” Skalsky said.
Something much lighter, made to meet Max’s challenges, would be necessary. But because no two AFM patients experience exactly the same issues, there was no real incentive for a company to invent the right product and start selling it on the open market.
A custom solution designed and built just for Max was what was needed, and Skalsky thought he knew just how to get the job done without breaking the bank.
In September, he submitted an application to UC San Diego’s Jacobs School of Engineering, which requires all seniors in its mechanical and aerospace engineering program to complete a capstone course, teaming up to solve real-world problems.
The challenge was accepted, and four students were assigned to spend just 10 weeks fabricating a solution.
The team learned they would need to come up with a way not just to minimize weight by using ultralight components but also to transfer that weight to Max’s torso.
Using 3-D printers and computer simulation, the team made prototype after prototype, tweaking designs for a harness, arm braces and other components until they had something that worked well enough to be machined in lightweight aluminum and sewn together by a professional seamstress.
The team sourced ultralight motors capable of generating enough force to lift more than a pound while weighing about as much as a ballpoint pen. Special sensors capable of being built into custom gloves were able to detect the motion of Max’s wrists, and a microcomputer loaded with custom computer code translated the data from the wrist sensors into smooth motion of the actuators.
Sourcing the right materials and writing the correct algorithms was just one piece of the challenge, student Marcos Serrano said. Bringing together disparate components around a growing boy was the real challenge. This design had to be flexible enough to grow with him, durable enough to survive his many adventures and comfortable enough to be worn all day, every day.
“This is what is called human-centered design,” Serrano said. “It was very important not just for it to work, but he had to be able to get it on and off easily, and he had to be able to actually use it.”
Max showed off his new range of motion Friday, tilting his wrists and getting an immediate response from the actuators at his elbows.
Asked by strangers what he intended to use his new motorized arms for, his response was nonverbal, feet running forward, torso twisting to deliver a solid punch with a sly smile.
Watching the show unfold, Kitty Cheung, Max’s mom, marveled at how far her son has come. The first sign of trouble came with a strange droop to one side of Max’s face, almost like the then-2-year-old had suffered a stroke.
“It was very sudden, and it was very scary. We didn’t know what it was, but it came on so fast,” she said.
Not long after that, she said, the arm paralysis began, followed by such weakness of the diaphragm that the toddler could not breathe on his own. Doctors kept him on a ventilator for a year before he recovered enough for the breathing tube to be removed.
Skalsky said the amount of nerve damage caused by AFM varies wildly but generally comes all at once. Nerves either die or survive, and those that make it have an amazing ability to adapt, in some cases filling in for those that were lost.
“As long as some functional nerves remain, they can split and kind of enervate where the old nerve was. Of course, if you have no nerves left, there is nothing to branch,” Skalsky said.
This year, there are about 100 senior engineering undergraduates in capstone classes, carrying out 24 projects, said David Gillett, a professor in the department of mechanical and aerospace engineering at UCSD’s Jacobs school.
The range of problems solved is eclectic, from creation of sensing equipment capable of detecting the inebriation level of lab mice being used in alcoholism research to an ultralight exam table small enough to fit inside a backpack and designed to allow field gynecological exams by healthcare workers in rural India.
Still working in industry for an Irvine-based medical device company, Gillett said there is simply nothing better than getting to work with engineering students at the moment at which they get to turn years of theory into projects capable of solving problems in the real world.
“It just fills me up,” he said. “I do it because I get to spar on a daily basis with whip-smart 20-something minds. It keeps you on your game, I’ll tell you that.”